Packaging Artwork Services
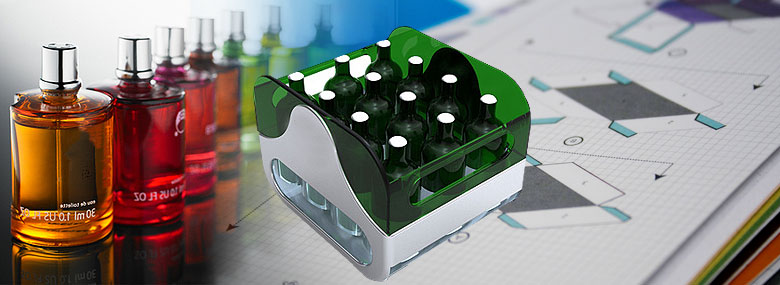
OMNiON Packaging Artwork Services
OMNiON provides a full range of packaging artwork services using state-of-the-art technology at the greatest value anywhere in the world.
Color Separation / Reseparation for Print
UCR
UCR or Under Color Removal is used whenever large percentages of three process inks are together to form a color, resulting in a substantial neutral or grey component. That is to say, past a certain point, adding more of one of the C, M, or Y process colors simply darkens the result. So, instead of simply adding more color, the UCR formula uses black ink to replace a partial amount of the other process colors in the shadow areas and in neutral colors. For example, in a screen tint build of 50% cyan, 40% magenta, and 45% yellow, magenta acts as the greying process. So, the 40% magenta value indicates the largest potential amount of black that can be added in place of a percentage of some of the other colors.
GCR
GCR or Gray Component Replacement is a specialized form of under color removal which involves a more general replacement of chromatic inks – not just the close to neutral ones as with UCR. In a GCR separation, black is substituted for a partial amount of the process colors in all areas where the three chromatic colors are present – even in lighter tones. That added range of color where CMY can be replaced with black is the key to how GCR reduces CMY ink usage.
The difference in the range of the black channel makes it fairly easy to determine whether UCR or GCR was used to create a particular CMYK separation. With a UCR separation the black printer appears as a “skeleton” image usually missing tones around the 0%-30% range while the CMY looks very colorful. In contrast, the black printer in a GCR separation looks more like a full range greyscale image while the CMY looks washed out.
Color Gamut Correction / High DMAX / Total Ink Coverage
We set up the color reproductions so that the colors are implemented efficiently within the printable density ranges so your brand’s identity is printed accurately. Both UCR and GCR separation techniques use a defined parameter to limit the maximum amount of ink that will be used in the darkest part of the image. This maximum total dot percentage is referred to as either TIC (Total Ink Coverage) or TAC (Total Area Coverage) and is determined according to the type of presswork and substrate that the images will be used for.
The combined value of all CMYK inks for a particular area or object cannot exceed a specified amount, or ink may not transfer effectively and printed sheets may not dry properly. This specified amount, referred to as Total Area Coverage (TAC), typically is limited to 300 for offset lithography using coated paper. Technically speaking, the TIL/TAC/TIC value should not exceed 300, depending on print process.
Trapping
Trapping involves creating overlaps (spreads) of objects during the print production process to eliminate misregistration on the printing press. Mainly used where coloured graphics such as text and images appear on a coloured background. Using trapping correctly greatly enhances the quality of the print and make the printers life a lot easier to produce quality work.
Overprint
Overprint is similar to trapping, but refers to the process of printing one color directly on top of another, in most cases this is black printing on a background colour. Other colours can be overprinted but be careful, combinations of colours can produce different results than otherwise planned. For example if you overprint Cyan on a Yellow background, the overprint will appear green.
Bleed
As with most processes there is a small amount of movement when the final printed job is being cut to size, whether this is digital sheets cut on a guillotine or larger sheets being die cut. To avoid unsightly white edges we include ‘bleed’. This is the area beyond the artwork which is cut off after printing. If the graphics or background colour is right to the edge of artwork, a 3mm ‘bleed’ ensures that no white of paper is showing if the guillotine is slightly off.
Resolution
To achieve the best results possible all artwork must be CMYK, 300dpi and of suitable print quality at the finished size. Low quality images will produce a blurred or pixelated result.
Spell Check
We help you avoid embarrassing mistakes by thoroughly checking the text for grammatical and spelling errors, which always get noticed after the job has been printed and nearly always require reprinting.
Fonts
Also known as typefaces, they can be one of the biggest causes of problems when creating artwork. Which is why we supply artwork in a print ready PDF format, which avoids the need to have the font/typeface supplied.
Font Outlines
Converting all fonts to outlines avoids any font issues when your packaging is printed. The accuracy of the final product cannot be guaranteed for artwork whose fonts have not been converted to outlines artwork.
Packaging companies benefit from the OMNiON’s packaging printing expertise when dealing with packaging artwork. This knowledge, combined with project and process management reduce steps during package production while optimizing workflows and quality. All packages are assembled 100% digitally using the latest ESKO Software Suite. This enables us to use the latest developments in printing technology which reduces the customers overall cost while improving the quality and turn around time of each finished package.
Please contact us at Packaging@OMNiON.biz for more information.
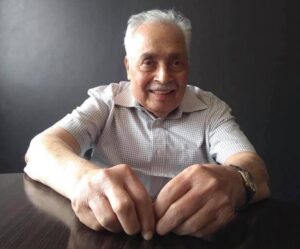
Our unique innovations & turn-key solutions based on our extensive experience & depth of knowledge will help you succeed. Our founder, M. C. Abraham, is India's most experienced, successful & widely regarded publishing & media services outsourcing expert having pioneered the y back in 1974 & our co-founder, Mat Abraham, managed media solutions technology for Quad/Graphics, USA with over 20 years experience serving all the top media & brand customers in the world.
Best Location